Timber frame homes and off-site construction are the future, says Frame Homes development manager Tom Dodd. We asked him why – and explored how the company’s relationship with MiTek is proving to be key to the housebuilder’s enduring and impressive success story.
Tom is a man who is clearly passionate about creating peoples’ dream homes. Most days on his way to work he’ll drive past one of his projects. And they all have one thing in common: they are built from timber frames.
Timber is in Tom’s blood and his love for ‘all things timber’ began from an early age when he trained as a carpenter. It’s no surprise, then, that today Tom is development manager at Frame Homes, the South West’s largest timber frame homes company.
Over the last decade, Tom has played an integral role in the construction of some of the region’s most progressive timber frame home developments, most recently the West Carclaze Garden Village in St Austell – the first garden village in a generation. Once complete, it will be one of the first Zero Carbon estates in the UK, and home to 1,500 families across its 500 acres of green space, lakes, flora and fauna.
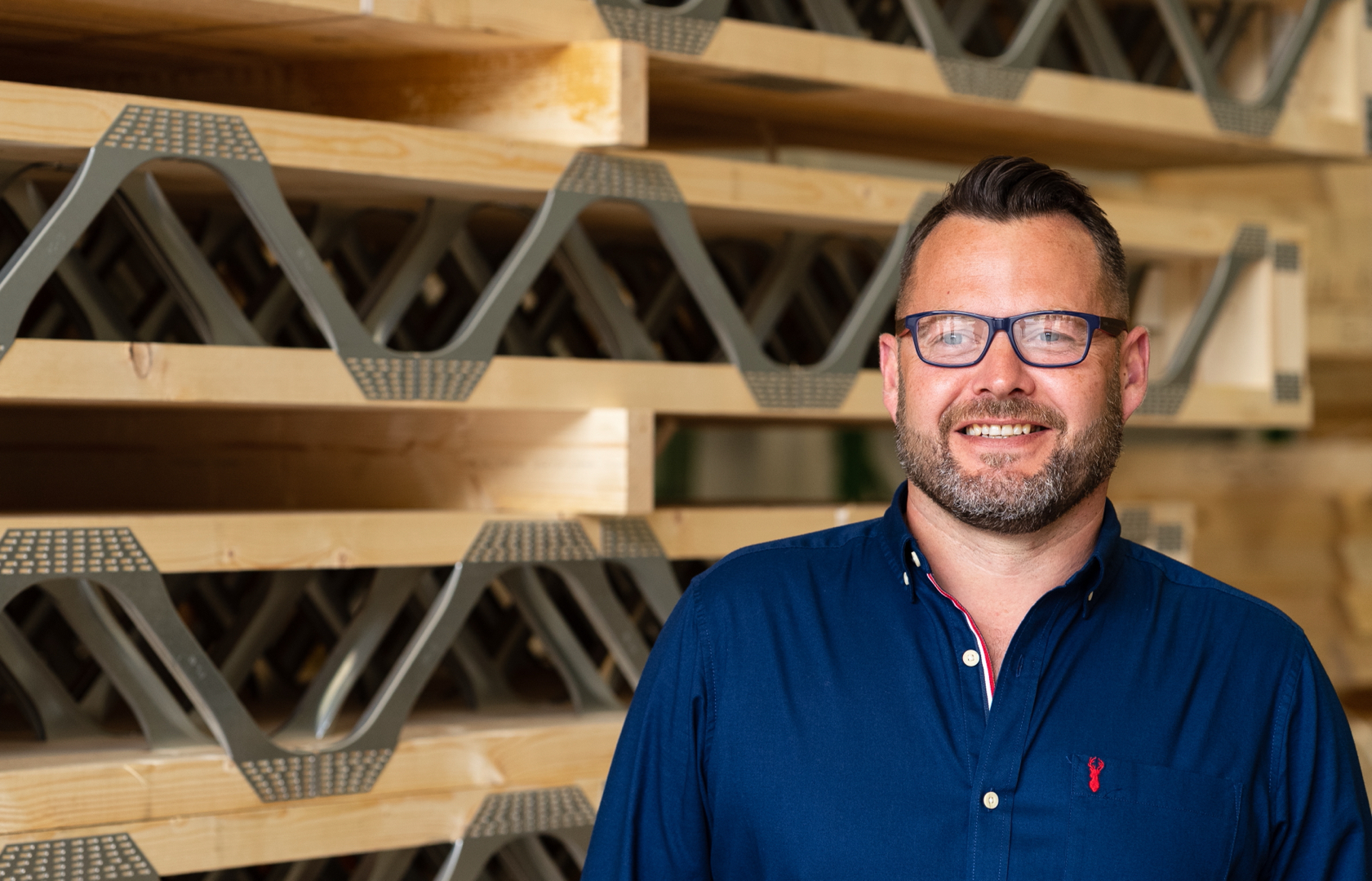
From humble beginnings
Frame Homes has been in the business of building homes since 1974. Now one of the largest and longest-standing timber frame manufacturers in the UK, its 100-strong team has created tens of thousands of homes for self-builders and small to medium developers through to housing associations – on projects ranging from major multi-home schemes to one-off unique homes.
What started with just seven employees in a small workshop in Perranporth almost half a century ago quickly grew into a high-scale operation, renowned for its high-quality timber frame construction. And MiTek was instrumental in earning them this reputation, as Tom explained.
“We were the first UK timber frame company to invest in MiTek’s High Speed Posi Press. It was the market-leading piece of machinery, offering much faster manufacturing, and the first of its kind to be installed in Europe.
“There was no way we could manufacture the number of joists we required without the high-speed Posi press. The increase in production from using it was phenomenal.”
Frame Homes has never looked back and today, it operates the largest fully-automated factory in the south west on a 4.5-acre site.
Investment in the Posi-Press was clearly a game-changer for Frame Homes, but it wasn’t the starting point for the relationship with MiTek, says Tom. It was already using MiTek’s sophisticated software which has helped it to push design boundaries and create homes that draw together expert engineering and style excellence.
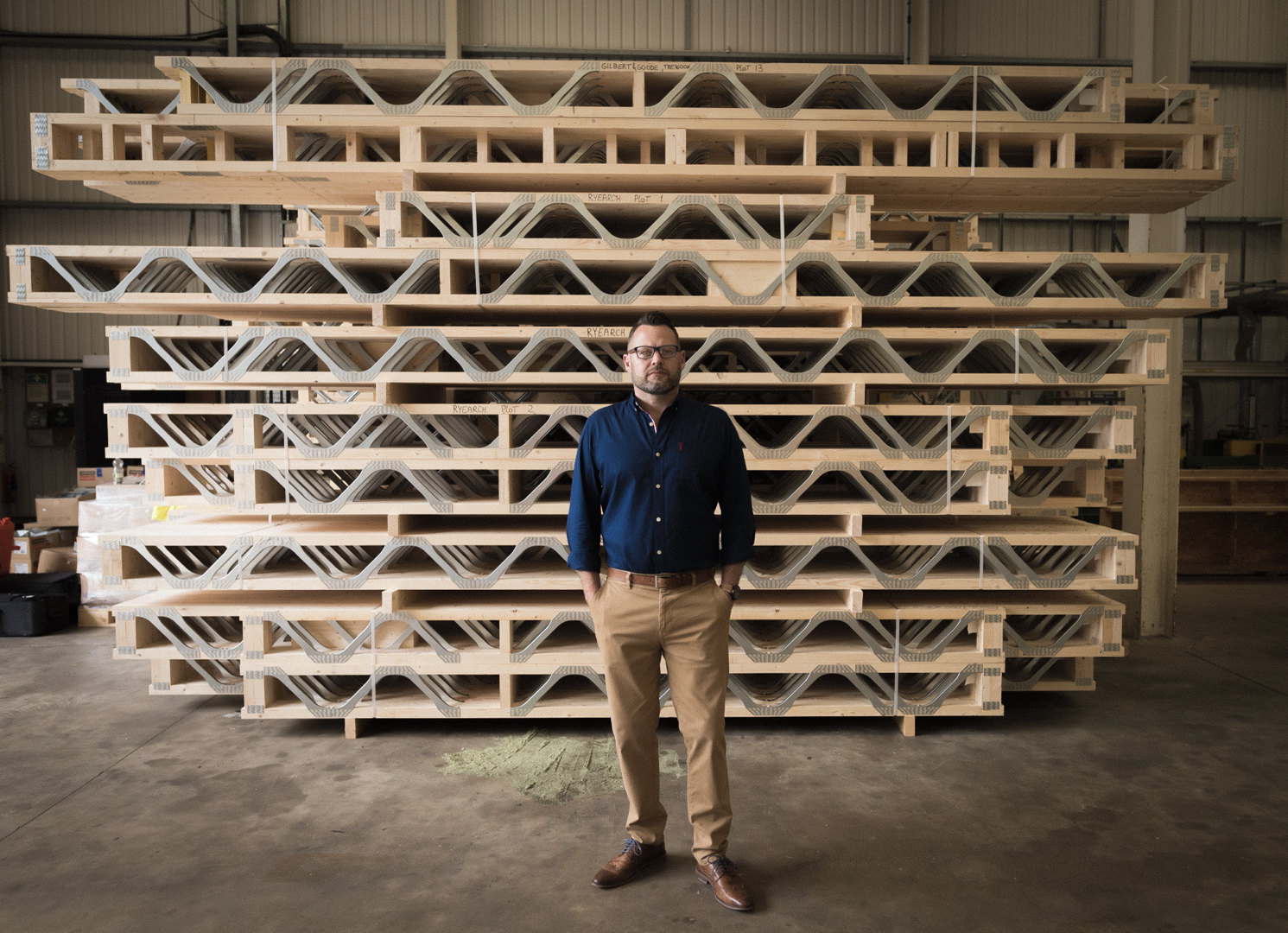
Seeking innovation and excellence
Frame Homes has always prided itself on searching out new ways of delivering construction innovation and excellence, a drive which began with its founder Bob Pepper and is shared today by Tom and his colleagues.
“We’re always looking to push the boundaries and MiTek has a shared appetite for this,” said Tom. “Their software programs, like WoodEngine which we’ve been using since 2011, are instrumental in enabling us to continue to improve and grow.
“From a timber frame design point of view using MiTek software was the best move we could have made. Unlike other pieces of software, the development never stops.
“Any particular development requests we have are addressed straight away. MiTek’s own designers all feel part of our family and we have easy access to their friendly helpdesk when we need it.
“What’s crucial for us as a manufacturer is the software performance, for the styling and the engineering of the products, and that really is where MiTek lead the line.”
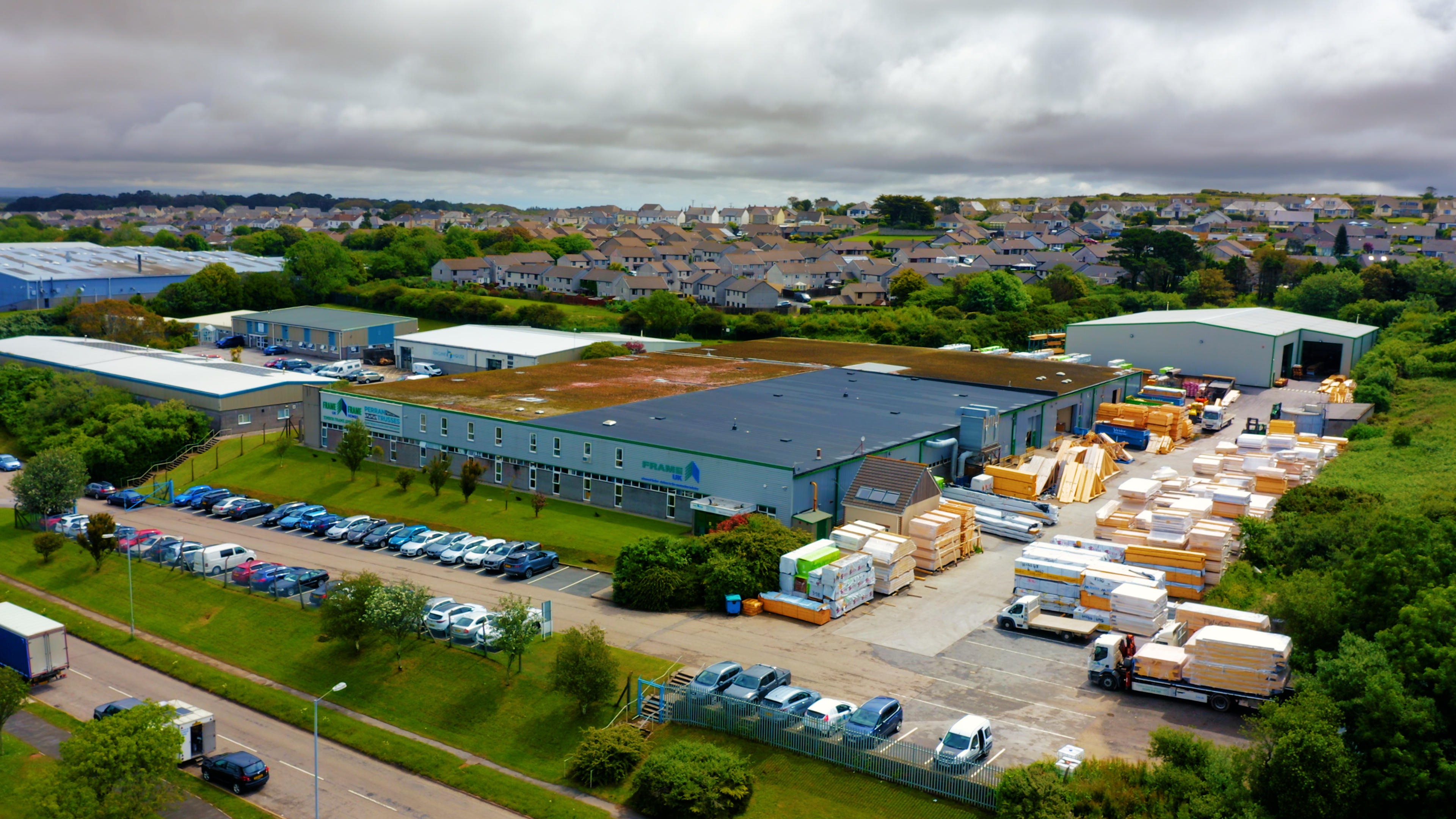
Investing in innovation and the power of partnership
Tom says Frame Homes’ enduring success is down to its reliability, attention to detail, and a determination to always be at the forefront of product development.
“You need to strive to find new solutions,” says Tom. “Our relationship with MiTek is rooted in this – with a shared desire to innovate and be ahead of the curve.”
It’s not just WoodEngine software from MiTek which has helped Frame Homes build such a thriving business. They’ve also used MBA, and more recently, Pamir, to help with roof truss and Posi-Joist design.
Tom says the partnership they’ve built with MiTek over the years has undoubtedly helped Frame Homes become a better business.
“Having worked together for 20 years, we’ve built a good understanding which brings great benefits for both parties, and I think it’s helped both businesses improve. It’s certainly helped us improve our operational performance and build a more efficient design and manufacturing process.
“And we’ve been able to benefit from MiTek’s new software offerings – they continue to invest in their programs which means we’re always getting the best service and support.”
“I like to push boundaries. I like to make a difference. Our relationship with MiTek helps me to do that.”
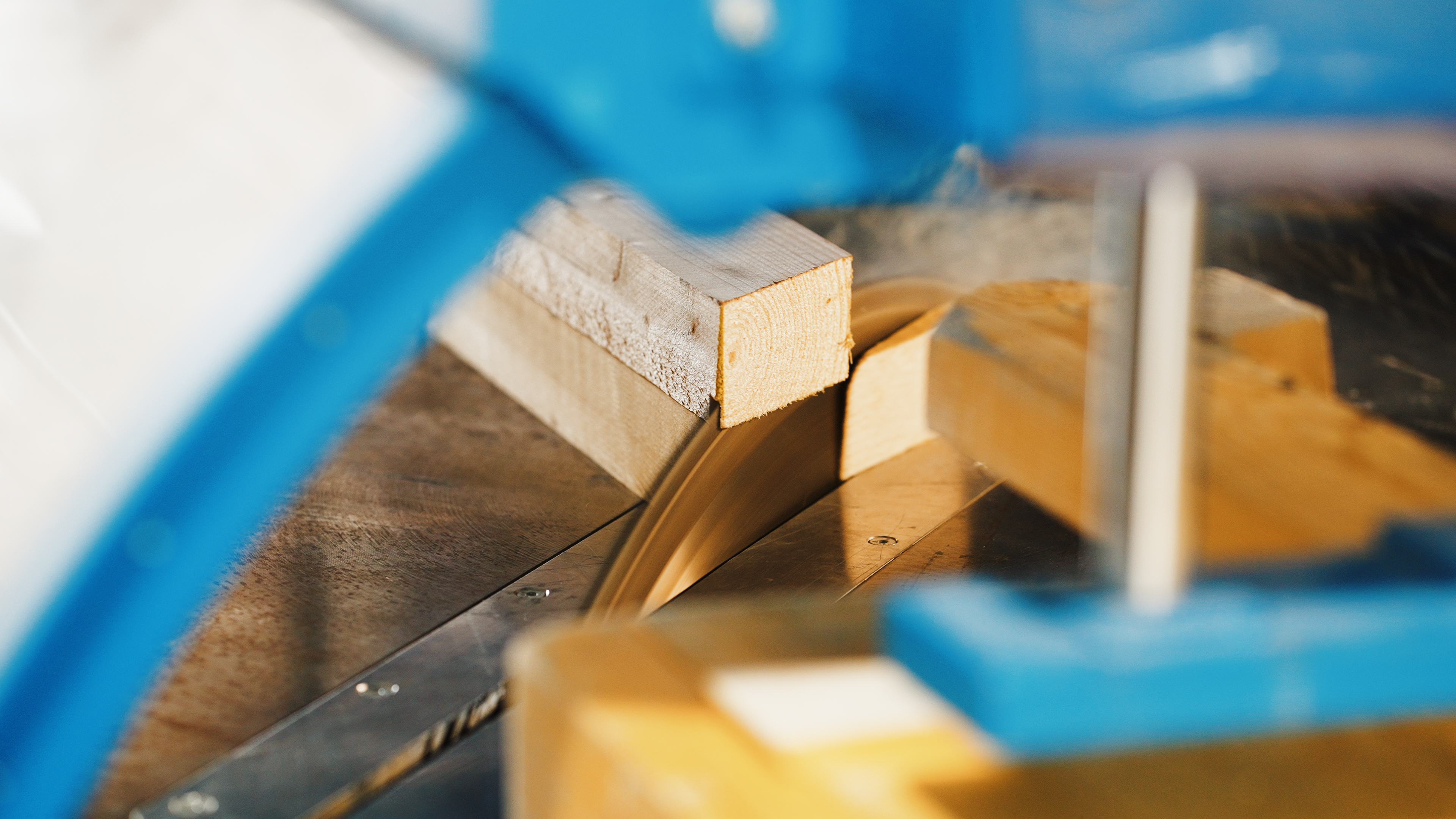
The future: timber frames and MMC
Tom notes that timber frame construction has been a fast-growing industry for the last decade. “With the drive for off-site efficiencies and sustainable construction this will continue to grow,” he says, insisting that the future is most definitely timber frame.
“Without a shadow of doubt. There are no more sustainable methods of construction in the UK.”
Timber frame construction is also quicker than masonry-based builds, typically by between 30-40%. “The West Carclaze development hasn’t got any masonry, so we estimate construction could be up to 50% quicker.
“Whilst timber frame is quite commonly a little more expensive than masonry, the offset in speed very much offsets the difference in cost. Aside from that, you wouldn’t be able to get anywhere near the kind of standards of installation within conventional masonry building. It’s not doable.”
The increasing drive to have zero carbon homes ready by 2025, combined with the national housing shortage and site skills shortage means MMC is the only way the country’s demands can be met. And this is an important point. MiTek’s Posi-Joist is playing an integral part in delivering sustainable homes.
“With the government’s housing programme focusing on low-energy solutions, it’s essential that we continue to look down different routes, such as the introduction of pre-insulated wall panels, which we were the first to bring to the market,” said Tom.
“Sustainability can’t be a tick box exercise any more. There’s still a national shortage of housing. It has to be delivered. It has to be sustainable. At the end of the day, timber frame is always going to be the most cost-effective, greenest way of building affordable homes.
It’s not just Frame Homes who believe timber frames are the future. Countless studies confirm this, the most recent one in 2018, which shows closed panel timber frames are the most cost-effective way of delivering housing for the UK.
As a society we have to respond at pace, says Tom.
“We always try to lead clients down the most sustainable route for their projects – not just using timber frame, but also things like eco-friendly friendly insulation, which comprises 89% recycled glass.
“And modern homes utilising MVHR capitalise on the versatility of Posi-Joist for duct routing, so MMC will be critical to meeting the growing demand for greener homes.
“We are also continuing to invest in the latest automated machinery, incorporating advanced IT technology to streamline our manufacturing.”
West Carclaze: a perfect example
What Tom loves most about his job is the opportunity to play a role in a number of varied schemes, from peoples’ dream self-builds to eco-friendly low carbon affordable projects like West Carclaze in the historical china clay landscape of St Austell, not far from the Cornish coast.
West Carclaze is destined to be different, and so is its design and build. Once complete, the 1500 home scheme will be one of the first carbon net zero developments in the UK.
Set in 500 acres, every home will be at the leading edge of energy efficiency and sustainability, with clever but discreet ‘under skin technology’, generating power and managing the temperature and air quality, so that people can live healthy and happy lives with a clear conscience.
“MiTek worked really closely with us to help design the best solution for the scheme”, says Tom.
“Using Posi-Joist at West Carclaze’s was key. The client is putting mechanical heat and ventilation systems into every unit, so the versatility of the Posi-Joist, allowing services to pass freely through the floor platform was absolutely essential. Also giving the client a really quality product.”
The homes are highly energy efficient using clever design, new technologies and innovative materials to reduce the need for heat whenever possible. Every home is fitted with inset solar panels, with clever battery backup to store it for later use.
Innovation is part of Frame Homes DNA, and at West Carclaze the team bought a new hybrid THERMO panel to the market for the development, which uses a different combination of environmentally friendly insultation and membranes to give a U-value of 0.12, which is down to passive standards.
“The new THERMO panels are, says Tom, very cost effective, because they’re manufactured on an automated production line. “It’s very quick and easy to put the insulation within the panel whilst horizontal on the line. And more importantly, any waste of installation, rather than going in a skip on-site, will go back to the manufacturers to get recycled and come back, and will be reused in a panel again,” he explained.
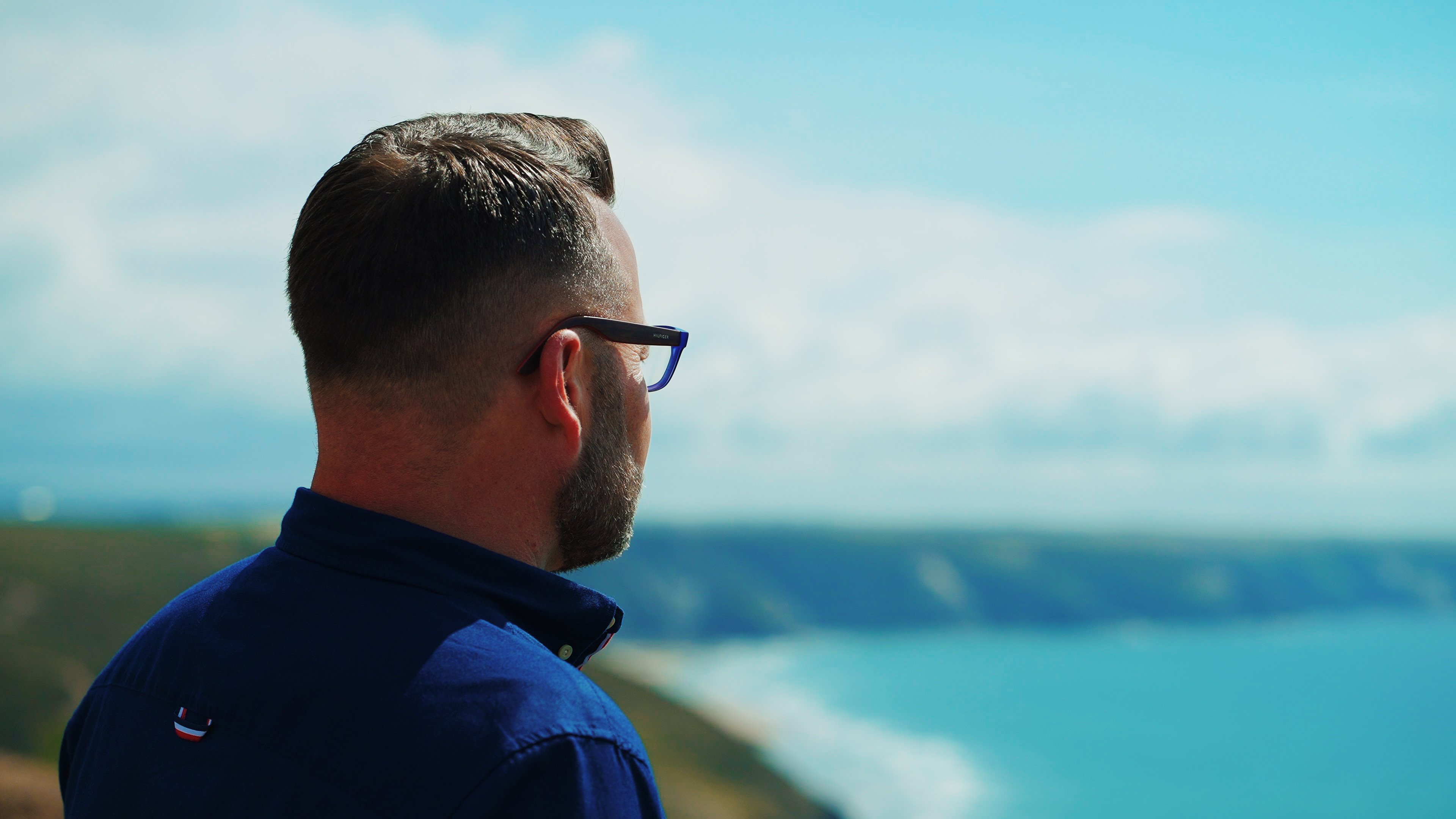
A healthy order book and a positive future
“We have built the business on repeat business and referral. Our reliability, attention to detail and always staying at the forefront of product development has maintained our popularity,” says Tom.
“It’s great that we have a very strong order book and the potential for more work to come our way for many years to come. We’re a Structural Timber Association GOLD ASSURE accredited offsite manufacturing facility, with ISO 9001 & ISO 14001 which gives clients the reassurance that the QA control that’s delivered via this route is second to none.”
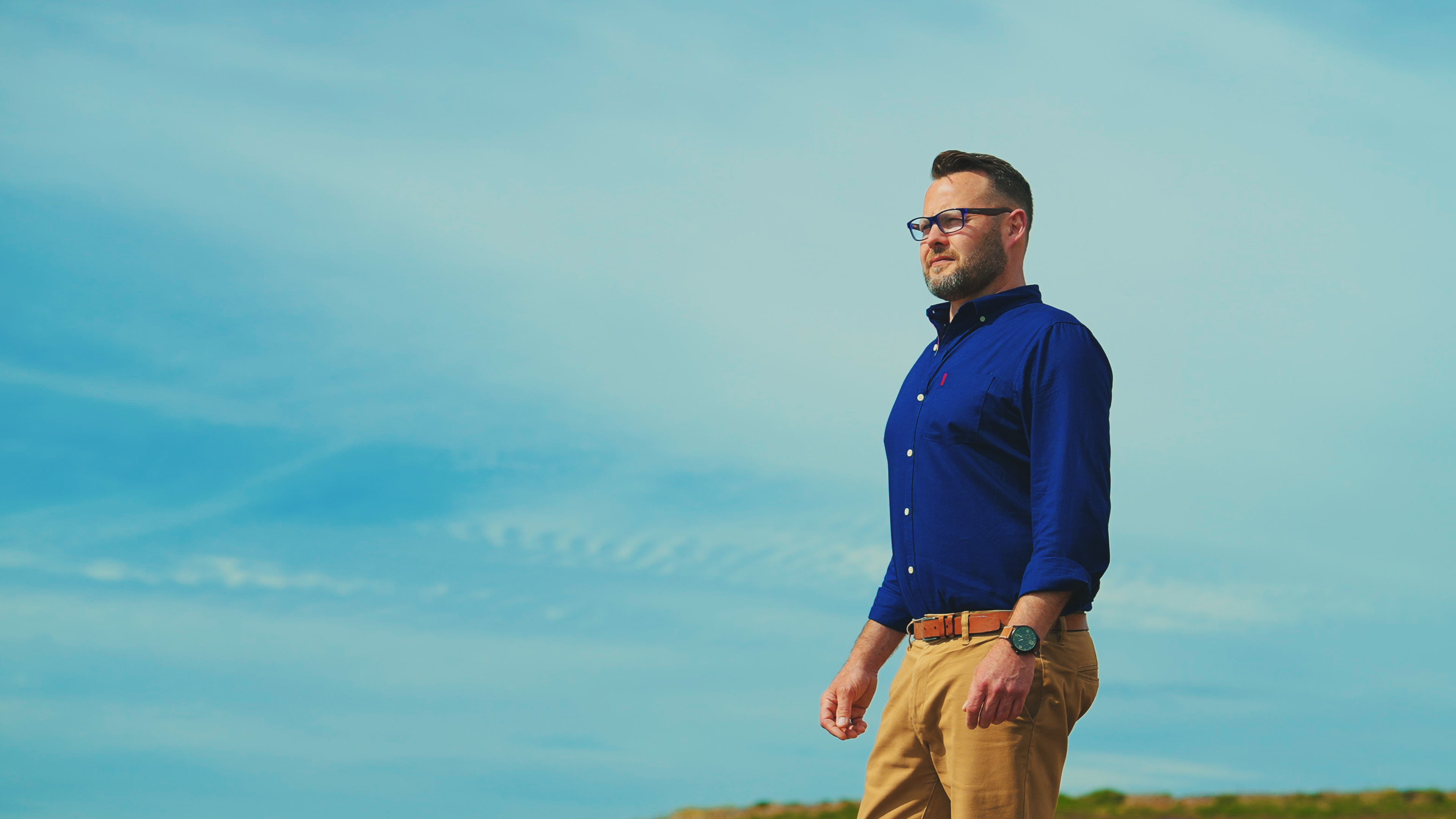